Что такое неравномерный прокат колеса
Обновлено: 25.06.2024
– излом колеса: по трещине у ступицы, по трещине у обода.
Любая из неисправностей этой группы независимо от места и размера – брак в эксплуатации и ремонте. В ремонте допускается устранение обточкой сетки термических трещин, если удается получить бездефектную поверхность металла.
В эксплуатации визуальным признаком наличия трещин являются: скопление валика из пыли и ржавчины летом, наличие иголок инея более высоких по отношению к другим зимой; при остукивании в зоне трещины - глухой звук при отжатых тормозных колодках.
Есть варианты контроля, хотя и менее точные, определения глубины ползуна с помощью линейки по его длине, в случае, если абсолютный шаблон
Зависимость длины ползуна от его глубины Таблица 4
Длина ползуна, мм | ||
Глубина ползуна, мм | 0,7 | 1,5 |
Неисправности вагонных осей в эксплуатации Таблица 5
Наименование неисправности | Причины возникновения | Способ определения |
Протертость средней части оси | Несоблюдение требований содержания тормозной рычажной передачи | Кронциркуль и линейка как полуразность диаметров в месте протертости и рядом с ней. |
Маломерность оси по диаметрам | Удаление металла при механической обработке, проворот колец, протертость. | Измерением диаметров микрометрическими, рычажными скобами, кронциркулем и линейкой |
Сварочные ожоги | Несоблюдения требований выполнения сварочных работ на вагоне. | Визуально. |
Изогнутость оси | Деформация от ударов при авариях и крушениях. | Измерение штихмасом между внутренними гранями колес в четырех диаметрально противоположных точках или проверкой на биение в центрах станка |
Неисправности колесной пары в эксплуатации Таблица 6
Наименование неисправности | Причины возникновения | Способ определения |
Сдвиг ступицы колеса на оси | Нарушение технологии формирования, удары при крушениях и авариях | Внешний осмотр. |
Признаки ослабления ступицы | Нарушение технологии формирования. | Внешний осмотр. Разрыв и вспучивание краски в месте соединения колеса с осью, выделение ржавчины и масла из-под ступицы с внутренней стороны колеса. |
Расстояние между внутренними гранями колес не соответствует | Сдвиг колеса на оси или результат обточки внутренних граней колес. | Штихмасом у свободно стоящей колесной пары в четырех точках. Максимальное и минимальное значение сравнивают с допуском. |
3 Нормативные требования к колесным парам вэксплуатации
Нормативные требования приводятся в таблице 7.
Допускаемые нормативы браковки в эксплуатации Таблица 7
Продолжение Таблица 7
Тонкий гребень | Для кол. пар грузовых и пассажирских вагонов при скорости движения до 120 км/ч – не менее 25 мм. При подготовке к перевозкам для грузовых вагонов – не менее 26 мм Для кол. пар пассажирских вагонов: - при скоростях движения 120-140 км/ч - не менее 28 мм; - при скоростях движения 140-160 км/ч - не менее 30 мм |
Тонкий обод | Для кол. пар грузовых вагонов– не менее 22 мм; Для кол. пар пассажирских вагонов: - при скоростях движения до 120 км/ч - не менее 30 мм; -при скоростях движения 120-140 км/ч - не менее 35 мм; - при скоростях движения 140-160 км/ч - не менее 40 мм. |
Ширина обода | В ремонте и эксплуатации допускается не менее 126 мм. |
Ползун | Допускается в эксплуатации глубиной не более 1 мм. |
Навар | Допускаемая высота навара в эксплуатации: - для грузовых колесных пар – не более 1 мм; - для пасс. колесных пар – не более 0,5 мм; |
Выщербина | Допускаемые размеры в эксплуатации: - для грузовых колесных пар – не более 10 мм по глубине и не более 50 мм по длине; - для пасс. колесных пар – не более 10 мм по глубине и не более 25 мм. Выщербина глубиной до 1 мм не бракуется независимо от длины. При наличии трещин в выщербине, идущих в глубь металла – колесо браковать независимо от размера. |
Местное уширение обода | В эксплуатации допускается не более 5 мм. |
Откол от наружной грани обода | Допускается в эксплуатации глубиной не более 10 мм, при этом оставшаяся ширина обода в месте откола допускается не менее 120 мм. |
Протертость средней части оси | Допускается в эксплуатации глубиной не более 2,5 мм, при этом минимальное значение диаметра в средней части должно быть не менее 165 мм. |
Маломерность оси по диаметрам | Ось бракуется если: - диаметр шейки – менее 130,005 мм; - диаметр предподступичной части – менее 165, 02 мм; - диаметр подступичной части – менее 182 мм; - диаметр средней части – менее 165 мм. |
Расстояние между внутренними гранями колес | Допускаемые размеры при подкатке: - для грузовых и пасс. колесных пар при скоростях движения до 120 км/ч – 1437-1443 мм; -при скоростях движения выше 120 км/ч -1439-1443 мм. |
В связи с указанием об ужесточении требований к колесным парам в зимних условиях, размеры допусков по дефектам уменьшить в два раза , если толщина обода менее 35 мм.
4. Расположение специального мерительного инструмента при измерениях неисправностей колесных пар в эксплуатации
Рисунки поясняют порядок измерений согласно таблицы 3
70 мм |
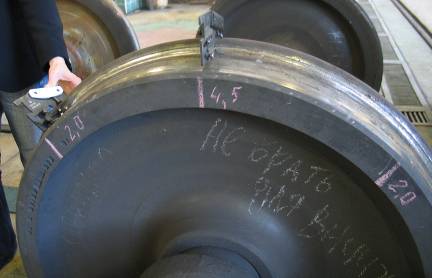
до 500 мм |
до 500 мм |
Рисунок 1- Измерение равномерного Рисунок 2 – Схема снятия замеров при проката неравномерном прокате
Рисунок 3 – Браковка гребня по толщине с помощью контрольного выреза
Рисунок 4 – Измерение фактического значения толщины гребня
Рисунок 5 – Контроль вертикального подреза гребня
Рисунок 6 – Зона браковки остроконечного наката гребня
70 мм |
Рисунок 7 – Измерение толщины гребня
Рисунок 8 – Измерение глубины ползуна по его длине
Контрольные вопросы
1. Укажите максимально допускаемый равномерный прокат в эксплуатации под пассажирскими вагонами со скоростями движения более 120км/ч
3. Укажите максимально допускаемый равномерный прокат в эксплуатации под пассажирскими вагонами дальнего следования при скоростях движения до 120км/ч
4. Укажите максимально допускаемый равномерный прокат в эксплуатации под рефрижераторными вагонами
5. Укажите максимально допускаемый неравномерный прокат в эксплуатации под грузовыми вагонами
6. Укажите максимально допускаемый неравномерный прокат колесных пар с редукторно-карданным приводом в эксплуатации
7. Укажите максимально допускаемую глубину кольцевой выработки на уклоне 1:20
8. Укажите максимально допускаемый равномерный прокат в эксплуатации под грузовыми вагонами
9. Укажите максимально допускаемую глубину кольцевой выработки на уклоне 1:7
10. Укажите максимально допускаемую ширину кольцевой выработки
11. Укажите минимально допускаемую толщину обода грузовой колесной пары
12. Укажите минимально допускаемую толщину обода пассажирской колесной пары со скоростью движения до 120 км/ч
13. Укажите минимально допускаемую толщину обода пассажирской колесной пары со скоростью движения от 120 км/ч до 140 км/ч
14. Укажите минимально допускаемую толщину обода пассажирской колесной пары со скоростью движения более 140 км/ч
15. Укажите минимально допускаемую толщину гребня грузовой колесной пары
16. Укажите минимально допускаемую толщину гребня пассажирской колесной пары со скоростью движения до 120 км/ч
17. Укажите допускаемые размеры выщербины для пассажирской колесной пары
18. Укажите минимально допускаемую толщину гребня пассажирской колесной пары со скоростью движения от 120 км/ч до 140 км/ч
19. Укажите допускаемые размеры выщербины для грузовой колесной пары
20. Укажите допускаемые размеры выщербины колесной пары, при которых она не бракуется по длине
21. Укажите случаи, при которых выщербина бракуется независимо от размера
22. Укажите максимально допускаемый размер ползуна
23. Укажите минимально допускаемую толщину гребня пассажирской колесной пары со скоростью движения более 140 км/ч
24. Укажите длину ползуна, при которой он имеет браковочную глубину
25. Поясните, как выводить с перегона колесную пару при наличии на ней ползуна глубиной более 1мм, но не более 2 мм
26. Поясните, как выводить с перегона колесную пару при наличии на ней ползуна глубиной более 2 мм, но не более 6 мм
27. Поясните, как выводить с перегона колесную пару при наличии на ней ползуна глубиной более 6 мм, но не более 12 мм
28. Поясните, как выводить с перегона колесную пару при наличии на ней ползуна глубиной более 12 мм
29. Укажите максимально допускаемую глубину протертости на средней части оси
30. Укажите максимально допускаемую высоту навара на колесных парах грузовых вагонов
31. Укажите максимально допускаемую высоту навара на колесных парах пассажирских вагонов
32. Укажите максимально допускаемую глубину выщербины на колесных парах вагонов
33. Укажите максимально допускаемую длину выщербины на колесных парах грузовых вагонов
34. Укажите максимально допускаемую длину выщербины на колесных парах пассажирских вагонов
35. Укажите максимально допускаемую длину выщербины на колесных парах пассажирских вагонов, при которой вагон можно довести до пункта формирования без снижения скорости
36. Укажите минимально допускаемую ширину обода в эксплуатации
37. Укажите максимально допускаемую высоту навара на редукторных колесных парах вагонов
38. Укажите максимально допускаемую глубину откола от наружной грани обода колеса
39. Укажите максимально допускаемое уширение обода колеса
40. Укажите минимально допускаемую ширину обода колеса в месте откола
41. Укажите признаки смещения колеса на оси
42. Укажите, в каком случае разрыв краски в месте сопряжения колеса с осью не является браковочным признаком
43. Укажите минимальный размер расстояния между внутренними гранями колес при эксплуатации со скоростями до 120км/ч
44. Укажите минимальный размер расстояния между внутренними гранями колес при эксплуатации со скоростями более 120км/ч
45. Назовите неисправность поверхности катания колеса, которая бракуется без проведения инструментального обмера (за исключением трещины)
46. Укажите допускаемую разность расстояний между внутренними гранями колес
47. Укажите признаки смещения колеса на оси
48. Укажите признаки наличия трещины в эксплуатации
49. Укажите мерительный инструмент и поясните методику измерения равномерного проката
50. Укажите мерительный инструмент и поясните методику измерения неравномерного проката
51. Укажите мерительный инструмент и место измерения толщины обода
52. Укажите мерительный инструмент и место измерения толщины гребня
53. Укажите мерительный инструмент и поясните методику измерения ползуна
54. Укажите мерительный инструмент и поясните методику измерения навара
55. Укажите мерительный инструмент и поясните методику измерения глубины выщербины
56. Укажите мерительный инструмент и поясните методику измерения глубины откола от наружной грани колеса
57. Укажите мерительный инструмент и поясните методику измерения протертости средней части оси
58. Укажите мерительный инструмент и поясните методику измерения разности расстояний между внутренними гранями колес
59. Укажите мерительный инструмент и место измерения ширины обода колеса
60. Укажите мерительный инструмент и поясните методику измерения глубины кольцевой выработки
61. Укажите мерительный инструмент и поясните методику контроля наличия подреза гребня колеса
62. Укажите мерительный инструмент и поясните методику измерения остаточной ширины обода в месте откола
63. Укажите мерительный инструмент и поясните методику измерения местного уширения обода
64. Укажите мерительный инструмент, который может быть использован при контроле глубины ползуна, если абсолютный шаблон и толщиномер отсутствуют
65. Укажите возможные причины образования выщербин
66. Укажите возможные причины образования ползунов
67. Укажите возможные причины образования наваров
68. Укажите возможные причины образования подреза гребня
69. Укажите базовые поверхности для установки на колесе абсолютного шаблона
70. Укажите, какие из неисправностей колес можно определить абсолютным шаблоном
71. Укажите, какие из неисправностей колес можно определить с помощью молотка
72. Укажите, какие из неисправностей колесных пар можно определить с помощью кронциркуля и линейки
73. Укажите, какие из неисправностей колес можно определить только толщиномером
74. Укажите, какие из неисправностей колес можно забраковать, пользуясь только линейкой
75. Укажите, какие из неисправностей колес можно определить толщиномером
76. Укажите, какой из специального мерительного инструмента предпочтительнее при измерении ползуна, абсолютный шаблон или толщиномер. Поясните почему.
77. Укажите признаки наличия на колесе неравномерного проката при встрече сходу и после остановки
78. Укажите рабочую поверхность гребня, на которой бракуется остроконечный накат гребня
79. Укажите возможные причины тонкого обода колеса
80. Укажите возможные причины откола от наружной части обода
81. Укажите возможные причины образования кольцевых выработок
82. Укажите возможные причины образования тонкого гребня
83. Укажите возможные причины образования остроконечного наката гребня
84. Укажите возможные причины образования равномерного проката
85. Укажите возможные причины образования неравномерного проката
86. Укажите возможные причины смещения колеса на оси
87. Укажите возможные причины образования подреза гребня
88. Укажите возможные причины образования местного уширения обода
89. Укажите возможные причины образования наплыва на фаску
90. Укажите возможные причины уменьшения расстояния между внутренними гранями колес менее допускаемого размера
Лабораторное занятие № 2
Тема: Исследование технического состояния буксового узла на соответствие требованиям в эксплуатации
Цель: изучить устройство специального мерительного инструмента для контроля буксовых узлов в эксплуатации, методы обнаружения неисправностей при техническом обслуживании буксовых узлов при встрече сходу и после остановки, научиться производить контроль букс и делать выводы о возможностях их дальнейшей эксплуатации
Ход занятия
1. Проверка знаний по нормативным требованиям к буксовым узлам в эксплуатации.
2. На предложенном варианте вагона или всего полигона произвести контроль состояния буксовых узлов остукиванием. Назвать возможные неисправности букс после проведения контроля.
3. Проверить указанные буксы шаблоном Басалаева. Сделать выводы на основании произведенных измерений.
Оформление отчета
1. Ответить на вопросы контрольной карточки с заполнением таблицы 8
№ карточки | 1 вопрос | 2 вопрос | 3 вопрос | 4 вопрос |
2. Ознакомиться с маршрутом обхода на полигоне. Подписать контрольный лист.
3. Согласно произведенного визуального контроля и остукивания, отметить на планшете номера букс, которые по вашему мнению являются неисправными.
4. Перенести номера неисправных букс на контрольный лист.
Теоретические сведения
Требования, запрещающие эксплуатацию буксовых узлов
Запрещается постановка в поезд и следование в нем вагонов, у которых буксовый узел имеет хотя бы одну из следующих неисправностей:
- ослабление болтового крепления смотровой или крепительной крышек буксы, вмятины смотровой крышки, выпуклости и протёртости её;
- повышенный нагрев верхней части корпуса буксы.
Неисправностями буксового узла с подшипниками кассетного типа, требующими отцепки вагона, являются:
- выброс смазки на диск и обод колеса, вызванный перегревом подшипников, наличие в месте переднего уплотнения равномерного валика смазки не является браковочным признаком для подшипников с адаптером;
- сдвиг корпуса буксы;
- обрыв болтов М20 или М24 торцевого крепления подшипников на оси;
- наличие воды или льда в корпусе буксы, выброс смазки в крышку смотровую, контролируемые при подозрении на неисправность подшипника после снятия крышки смотровой буксового узла;
- повышенный нагрев верхней части корпуса буксы или адаптера;
- температура нагрева верхней части корпуса буксы не должна достигать 60ºС, без учета температуры окружающего воздуха, и определяется с помощью бесконтактного измерителя температуры "Кельвин".
Колёсные пары относятся к ходовым частям и являются одним из ответственных элементов вагона. Они предназначены для направления движения вагона по рельсовому пути и восприятия всех нагрузок, передающихся от вагона на рельсы при их вращении. Работая в сложных условиях нагружения, колёсные пары должны обеспечивать высокую надёжность, так как от них во многом зависит безопасность движения поездов.
Основные неисправности колесных пар
Равномерный прокат колес - естественный износ поверхности катания обода. В результате уменьшается диаметр колеса и увеличивается высота гребня относительно поверхности качения. При большом прокате нарушается взаимодействие колеса с элементами стрелочного перевода при проходе крестовин. Поэтому глубина проката ограничена:
при скорости движения до 120 км/ч:
грузовые и рефрижераторные вагоны - не более 9 мм,
пассажирские в местных и пригородных поездах - не более 8 мм;
пассажирские дальнего следования - не более 7 мм
при скорости движения 120-140 км/ч:
пассажирские вагоны - не более 5 мм.
Равномерный прокат измеряют инструментом который называется “абсолютный шаблон”. Для измерения шаблон устанавливают на гребень колеса. отсчет на шкале вертикального движка. Цена деления 1 мм.
Неравномерный прокат колес - это прокат, характеризующийся различной глубиной по кругу катания колеса. Изменение глубины проката происходит плавно на расстоянии одной пятой и более длины круга катания колеса. Поэтому неравномерный прокат трудно выявить при осмотре колес под вагоном.
При наличии неравномерного проката увеличивается динамическое воздействие вагона на путь, поэтому ограничена разница между наибольшей и наименьшей величиной проката на одном колесе. Эта разница допускается в пассажирских поездах не более 2 мм, а в грузовых ( у грузовых вагонов) - более 3 мм.
Неравномерный прокат измеряют абсолютным шаблоном в месте максимального износа и с каждой стороны от этого места на расстоянии до 500 мм.
Тонкий гребень. Уменьшение толщины гребня происходит в результате его естественного износа в процессе эксплуатации вагона. Наименьшая толщина гребня ограничена, так как в случае тонкого гребня могут быть удары его в остряк стрелки при противошерстном движении. ПТЭ и инструкцией осмотрщику вагонов для скоростей движения до 120 км/ч толщина гребня, измеренная на расстоянии 18 мм от его вершины, установлена в пределах: не более 33 и не менее 25 мм.
По указанию МПС от 1995 г. № М 535 у развернутых колесных пар в эксплуатации допускается толщина гребня одного из колес не менее 23 мм, если у другого колеса толщина гребня не менее 25 мм.
Измерение толщины гребня производят абсолютным шаблоном. Для измерения шаблон устанавливают на гребне колеса и горизонтальный движок прижимают к гребню. Размер считывают на шкале под движком. Цена деления 1 мм.
Вертикальный подрез гребня. Износ гребня, в результате которого угол наклона гребня к его основанию увеличивается до 90° и на гребне образуется вертикальная площадка. Подрезанный гребень при движении по стрелке при противошерстном движении может ударить в остряк или при не подходе остряка взрезать стрелку. Поэтому величина вертикального подреза гребня ограничена. Оценку подреза гребня производят специальным шаблоном. Вертикальную подвижную ножку шаблона прижимают к внутренней грани гребня. Колесную пару не допускают к эксплуатации, если риска на движке шаблона, на высоте 18 мм от основания гребня соприкасается с подрезанной частью гребня.
Остроконечный накат гребня - выступ металла по круговому периметру гребня в месте перехода изношенной поверхности к вершине с выкружкой по радиусу 12,5 мм. Остроконечный накат опасен тем, что при противошерстном движении по стрелке колесо может накатиться выступом металла на остряк и перекатиться через остряк. Поэтому начиная с 1998 г. вагоны, у которых обнаружен остроконечный накат, отцепляют для смены колесной пары.
Выявление остроконечного наката колес производят визуально. Инструментального метода не существует, что является в ряде случаев причиной субъективной оценки этого вида дефекта.
Ползун - это плоское место или местный износ поверхности катания в результате скольжения колеса по рельсу. Образуется в результате заклинивания колесной пары при торможении или вследствие какой либо другой причины. Например, известны случаи заклинивания колесной пары в случае высокого нагрева неисправной буксы. Ползун может вызвать опасные последствия воздействия на путь. Может быть излом рельсов от ударов неисправного колеса или насечки на рельсах. Может быть сход вагона, в особенности на стрелочных переводах. Поэтому глубина ползуна- представляющая высоту сегмента изношенного места, в эксплуатации ограничена. В соответствии с ПТЭ ползуны, глубиной до 1 мм не бракуют. При обнаружении ползуна более 1 мм, но не более 2 мм, разрешается довести вагон до ближайшего пункта технического обслуживания вагонов, имеющего средства для смены колесных пар, со скоростью: пассажирский не свыше 100 км/ч, грузовой - не свыше 70 км/ч. На этом пункте вагон должен быть отцеплен для смены колесной пары.
При глубине ползуна свыше 2 мм разрешается следование поезда с перегона до ближайшей станции с ограничением скорости.
- -при глубине от 2 до 6 мм - со скоростью 15 км/ч.
- при глубине от 6 до 12 мм - со скоростью 10 км/ч.
- при глубине свыше 12 мм разрешается следование со скоростью 10 км/чс исключением вращения колесной пары (на тормозных башмаках). На станции у вагона должна быть заменена колесная пара.
Глубину ползуна определяют абсолютным шаблоном. Для этого измеряют прокат колеса рядом с ползуном и посередине ползуна. Разница этих измерений представляет глубину ползуна.
В случае отсутствия абсолютного шаблона глубину ползуна можно оценить измерив его длину.
Зависимость глубины ползуна от его длины.
Длина ползуна, мм | 50 | 60 | 75 | 85 | 100 | 145 | 205 |
Глубина ползуна, мм | 0,7 | 1,0 | 1,5 | 2,0 | 3 | 6 | 12 |
Навар - это смещение металла на поверхности обода колеса в виде выступа. Навар образуется при кратковременном проскальзывании колеса по рельсу на 20-30 мм. Не допускаются к эксплуатации колесные пары с наваром толщиной более 0,5 мму пассажирских и более 1 мм у грузовых вагонов.
В случае обнаружения навара более указанных размеров, но не более 2 мм на промежуточных станциях разрешается довести вагон до ближайшего пункта технического обслуживания вагонов, имеющего средства для смены колесных пар. При этом скорость движения ограничивают в пассажирских поезда не более 100 км/ч, в грузовых - не более 70 км/ч.
Определение величины навара производят абсолютным шаблоном. Измеряют прокат колеса на неповрежденном месте обода, рядом с наваром. Затем движок шаблона ставят на наплыв металла и считывают показание. Разница двух измерений даст толщину навара.
Местное уширение обода колеса - раздавливание обода и местный наплыв металла в зоне фаски с наружной грани обода. Опасный дефект, так как при пошерстном движении колесо с наплывом может не выкатиться на рамный рельс и будет раскантовывать путь. Поэтому в эксплуатации не допускается местное уширение более 5 мм.
Определяется путем измерения с помощью кронциркуля и линейки ширины обода в месте наибольшего уширения и в месте где нет уширения (без учета размера фаски).
Поверхностный откол у наружной грани обода. В результате откола уменьшается ширина обода и может быть опасность схода колеса в кривых участках пути с боковым износом рельсов. Поэтому запрещается эксплуатация вагона, если ширина оставшейся части обода в месте откола менее 120 мм. Колесную пару бракуют также если глубина в месте откола по радиусу колеса более 10 мм или в поврежденном месте есть трещина.
Откол кругового наплыва. Местный поверхностный откол кругового наплыва металла на фаску, выходящий за наружную грань обода. Требования к колесу такие же, как в случае поверхностного откола.
Излом колеса - разрушение колеса или откол и выпадение части колеса. Обычно по развившимся трещинам усталости металла.
Кольцевые выработки – запрещается выпускать в эксплуатацию и допускать к следованию вагоны имеющие кольцевые выработки у основания гребня или на участке пов-ти катания, с уклоном 1:20 глубиной более 1 мм и шириной более 15 мм, с укл. 1:7 глубиной более 2 мм и шириной более 20 мм
Виды ремонта колесных пар
В зависимости от вида неисправностей ремонт колесных пар осуществляют:
- без смены элементов,
- со сменой элементов.
Ремонт колесных пар без смены элементов.
При ремонте без смены элементов выполняют:
- обтачивание поверхности катания колес,
- наплавку гребней колес,
- наплавку поврежденной резьбы M 110,
- заварку изношенных центровых отверстий и отверстий для болтов стопорных планок.
При необходимости шейки и предподступичные части полируют абразивной шкуркой.
Дефекты на поверхности катания колес при ремонте устраняют механической обработкой на колесотокарных станках. Такой обработке подвергают поверхности катания, включая гребни и фаски. Внутренние грани обрабатывают в том случае, если разность расстояний между ними, измеренная в разных местах, составляет более 2 мм. Наружные грани разрешается обрабатывать при наличии поверхностных дефектов при условии, что не будут срезаны клейма завода-изготовителя, и ширина обода будет не менее 126 мм.
Форму профиля катания проверяют максимальным шаблоном, при этом:
- зазор между шаблоном и профилем колеса допускается не более 0,5 мм,
- по высоте гребня - не более 1 мм.
После наплавки, а также после механической обработки наплавленных поверхностей, производят неразрушающий контроль гребней методом дефектоскопии.
© 2014-2022 — Студопедия.Нет — Информационный студенческий ресурс. Все материалы представленные на сайте исключительно с целью ознакомления читателями и не преследуют коммерческих целей или нарушение авторских прав (0.006)
Размеры элементов колесных пар при выпуске вагонов из ремонта должны быть в пределах, указанных в Инструкции ЦВ 3429 (прил. 6, 7, 8). В табл. 2.2. приведены допускаемые размеры колес и колесных пар при выпуске их из ремонта. В процессе ремонта обрабатывают фаски, поверхности катания, гребни и при необходимости внутренние грани колес, если расстояние между ними в разных точках то более 2 мм. Для устранения поверхностных дефектов могут обрабатываться и наружные грани.
Допускаемые размеры колесных пар и их элементов _ при выпуске вагонов из ремонта_
Наименование элементов, параметров и дефектов колесной пары
Размеры, мм, при выпуске из ремонта
Текущего отце- почного
1. Расстояние между внутренними гранями ободов цельнокатаных колес у колесных пар грузовых и пассажирских вагонов в поездах обращающихся со скоростями до 120 км/ч
2. Расстояние между внутренними гранями ободов цельнокатаных колес у колесных пар грузовых и пассажирских вагонов в поездах обращающихся со скоростями более 120 км/ч
3. Разность расстояний между внутренними гранями ободов цельнокатаных колес (измерения в четырех противоположных точках), не более
4. Разность диаметров по кругу катания колес, насаженных на одну ось, не более
- 5. Толщина обода колеса, не менее:
- а) у вагонов в пассажирских поездах, следующих со скоростями от 140 до 160 км/ч
- б) то же, со скоростями от 120 до 140 км/ч
- в) то же, со скоростями до 120 км/ч
- г) у грузовых вагонов четырех-, шести- и восмиосных
6. Равномерный прокат колесных пар, не более:
а) у пассажирских вагонов, включаемых в поездах, обращающиеся со скоростями от 120 до 160 км/ч
Читайте также: